Automotive supplier implements enterprise-wide product safety changes
- Chuck Russell
- Nov 23, 2022
- 2 min read
Issue:
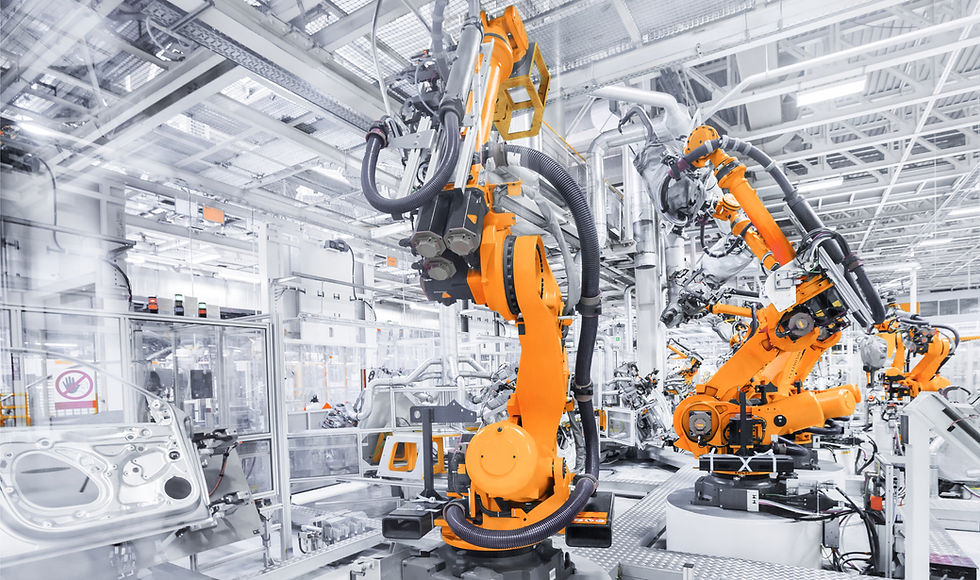
Automotive supplier desires to implement a rigorous product safety process to ensure all products produced are compliant with regulatory and customer requirements. Supplier was experiencing a number of “near misses” and the Board desired to make system improvements to enhance customer relationships and reduce business risk.
Implementation:
The Product Safety Process was developed with the goal to ensure all products manufactured and sold to OEM customers were free of safety defects and met all vehicle safety requirements set forth by FMVSS standards, NHTSA requirements and specific performance requirements called out by our customers. Led a cross functional team within the company to benchmark, develop and implement the Product Safety Process for the company and supply base.
The Product Safety Process was completed in 6 months and included processes to ensure designs were robust and compliant with requirements and DFMEAs. As well processes were put in place to ensure the manufacturing and quality controls within the company and the supply base were consistent with PFMEAs and required control plans. In addition to the engineering development changes and enhancements, changes were made to the supply chain requirements through documented PFMEAs, enhanced technical reviews, and required manufacturing controls.
The Product Safety Process also included a highly rigorous investigation process should an issue arise. The investigation process included a closed loop to drive lessons learned were adopted and KPIs were regularly reported to the Senior Leadership of the Company. These changes required the involvement, buy-in and implementation by the quality, manufacturing, supply chain, engineering and legal organizations.
Project was supported by Cornerstone’s strategic partner, David B Kandt Consulting.
Results:
1. The new Product Safety Process was highlighted in the company Social Responsibility report to the shareholder.
2. Product Safety process recognized and benchmarked by Automotive OEMs
Comments